What is a Warehouse?
A warehouse is a large physical structures used to store:
- Raw Materials and
- Finished Goods
Warehouses are used by various entities like, Manufacturers, Importers, Exporters, Distributers, Wholesalers, etc.., to maintain inventory of the goods they transact in.
What is Warehouse Management?
Warehouse management, is the process of organizing and running a warehouse in the most optimal way possible. This involves, having complete control over the operations carried out in the warehouse along with optimal management of inventory, following all safety standards and protocols to ensure protection of the goods stored in the warehouse, along with the warehouse personnel and equipment. Warehouse management also involves, providing and maintaining the facilities and equipment that are critical for operations. Facilities can include:
- Dock Levellers
- Material Handling Equipment like Fork Lifts, Order Pickers, VNAs, etc...
- Cranes or other special equipment for offloading/loading based on requirement
- Cold Storage/Temperature Controlled Zones
Typical operations carried out in a warehouse includes:
- Inbound Operations
- Outbound Operations
- Inventory Management
- Vehicle/Yard Management
- Location Management etc…
The operations, listed above can be handled either manually or by using a Warehouse Management System. Controlling and managing a large warehouse with complex operations manually is extremely resource intensive and often leads to errors in operations. To minimize the operational overhead and dependence on warehouse personnel to manage the operations and inventory in an optimal way, a warehouse management system can be implemented.
What is a Warehouse Management System?
A Warehouse Management System is a software solution that controls all the activities of a warehouse
- A WMS provides visibility and controls critical operations like:
- Inventory Management
- Location Management
- Receiving and Put-away
- Picking
- Sorting
- Packing
- Loading
- Invoicing and Dispatch
- Movement and Storage of Material in the Warehouse
- Inventory Reconciliation
- One of the major advantage of a WMS system is that it eliminates dependency on warehouse personnel in terms of inventory status and operational decisions:
- The system takes care of important functions like
- Location Suggestion
- Allocation Policies
- Guided Operations
In order to optimize operations within a warehouse
A bird’s eye view of a typical warehouse
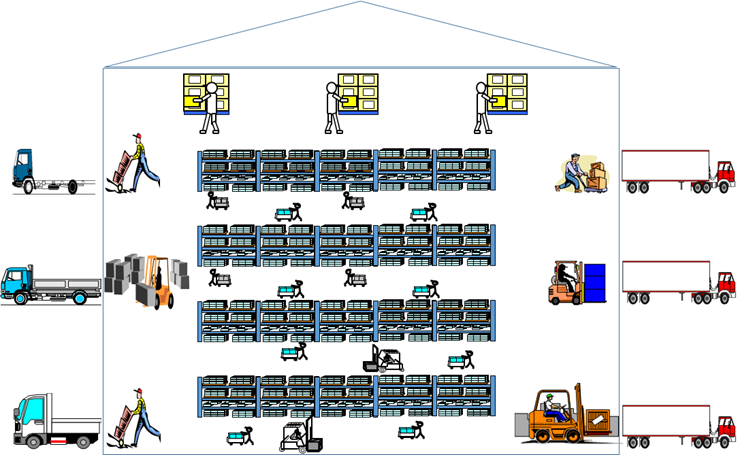
Let us look at how a warehouse typically works with a good WMS:
Inbound Operations:
- The inbound operations typically starts with creation of a ASN (Advance Shipping Note)
- The ASN will contain details like:
- Who is the supplier
- The Supplier Invoice Number
- The PO Number against which the delivery is being made
- SKU details
- Quantity and
- The UOM
- The ASN can also contain additional details like:
- Vehicle No
- Trailer No
- Estimated Time of Arrival (ETA)
Planning
- Based on the details enters in the ASN, the system generates a activity plan covering the following points:
- A schedule for unloading based on the type of vehicle and details available in ASN
- Resources required for unloading in terms of:
- Manpower
- Supervisors
- Laborers
- Specialist Operators for MHE’s
- Material
- MHE (Material Handling Equipment)
Vehicle In
- The next step is when the vehicle reaches the warehouse:
- Visualization screens displayed on the TV displays information like:
- Expected Vehicles
- Delayed Vehicles
- In-Premise Vehicles
- Parking Lot Status and
- Dock Status
- When the vehicle arrives at the warehouse:
- In case the vehicle details exist in the system:
- A license plate reader reads the license plate of the vehicle automatically and pulls up the details of the vehicle in the system
- The security person verifies the details in the system against the physical documents, records important checklist parameters and registers the vehicle in process and generates a Gate-Pass
- The system then redirects the vehicle automatically to an empty dock based on the dimensions, weight of the vehicle and the goods it is carrying
- In case no docks are available then the vehicle is redirected to the parking lot
- In case the vehicle details are not available and the vehicle has arrived for unloading:
- The security person enters relevant details in the system, records important checklist parameters and registers the vehicle in process and generates a Gate-Pass
- The system performs a Ad-hoc vehicle in and redirects the vehicle to an available parking lot
- A notification is sent to the relevant team in the form of an email or a message informing arrival of the vehicle
- The supervisor then creates a Express ASN against the vehicle
Docking, Receiving and Put-away
Docking
- Before starting the unloading process, the vehicle is docked and is prepared for unloading
- In case the vehicle is in the parking lot, the driver is informed through the following modes about reporting to the designated dock:
- A message is sent to the driver’s mobile
- A notification is displayed in the parking lot / drivers waiting area
- An announcement through a public address system
All of the above means of communication is controlled through the system
- The driver then reports to the dock along with his / her vehicle and the supervisor scans the vehicle to record the dock in time
- The unloading team then proceeds to unload the vehicle and also has an option to scan and unload the material if required
- Barcode labels, either linear barcodes or QR codes are printed at this stage, if required and applied to the shipment
- Post unloading / receiving, an automatic instruction is created and assigned to a receiving team
Receiving
- A notification is shown on the HHT of the receiving team about the new task assigned
- The receiving team then proceed to receive the items in the system using HHT operations
- Operation can be split into the following:
- Receive As-Is (loose)
- Receive As-Is (Pallets)
- Receive as loose and Put-away as loose
- Receive as loose and Palletize (With or without additional VAS activities like shrink wrapping)
- Receive as Pallets and put-away as loose
- Post receiving, a put-away task is generated automatically and a notification is displayed to the put-away team
Put-Away
- An automated guidance algorithm is employed by the system to decide in which bin which SKU and what quantity can be placed
- The location suggestion algorithm considers the following points among others to decide the bin:
- Reservations and Restrictions, if any
- ABC Value of the SKU
- SKU / Pallet Dimensions
- Weight of the SKU / Pallet
- The system also automatically suggests different locations for pallets and loose SKUs
- The system guides the put-away team to put-away the SKU’s in the designated locations by calculating the optimal put-away path using preset algorithms
- Feedback is provided to the operator at each stage during the guided put-away operation to ensure the SKUs are placed in the right locations and also to ensure that the put-away is completed in the minimum possible time
Resource and Activity Tracking
- At each stage of the operations, the system automatically captures and records all the activities carried out by the logged in users
- Additionally, the system captures resources in terms of:
- Manpower utilized
- Supervisors
- Laborers
- MHE
- Consumables
- Example
- Shrink Wraps
- SKU / Pallet Labelling
Outbound Operations:
Sales Order Processing:
- The outbound operations starts with creation of a sales order (SO) through one of the following modes:
- Screen
- CSV / Excel Upload
- Integration
- Post creation the SO is approved and the stock is allocated against an order
- During stock allocation the system ensures that:
- The SKU is assigned based on the allocation rule set for an SKU
- Allocation rules include rules such as
- FIFO
- FEFO
- FMFO
- Location Flush
- And combination of the above rules
- Apart from the allocation rule, the system ensures that ordered quantity is optimally allocated across different UOMs
Picking Instruction Creation
- Based on the ETA specified in the SO along with the lead time required for Picking, Packing, Loading and Dispatch processes, the system automatically creates a picking instruction and assigns the instruction to a picking operator
- In case the same team carries out both put-away and picking tasks, interleaving of tasks is used to opportunistically assign tasks to the operators to increase operational efficiency
- The system automatically chooses one of the following picking methodologies based on the order type and the type of SKU and the being picked
- Wave Picking
- Route Based Picking
- Bulk Picking
- Zone Picking
- Order Wise Picking
Picking:
- Post instruction generation, the picking task is automatically assigned to a operator and a notification is sent to the operator about the task
- An automated guidance algorithm is employed by the system to identify and guide the operator on the optimal picking path for the order(s) being picked
- The picking operator can execute the picking instruction using the following methodologies:
- Scan a Linear Barcode / QR code to pick the SKUs
- Use the inbuilt Voice Picking option to execute the instruction
- The picked items can then be moved to either one of the following locations based on operational needs:
- Sorting Area
- Packing Area
- Dispatch Area
Sorting Operation
- A guided soring operation is employed by the system to help sort SKUs belonging to different orders
- Either HHT based sorting or Sort to Light option can be used to sort the SKUs order wise
Packing Operation
- Post sorting the SKUs can be packed using HHT / Screen operations
- The SKUs can be packed in primary as well as secondary packaging, and further packed into transport packs
Preparing For Dispatch
- Post packing, the system identifies the best freight forwarder for the shipment based on different options like:
- Serviceability
- Pricing
- Volumetric Weight based or
- Fixed Charges
- Delivery Lead Time
- The system then integrates with the Freight Forwarder’s portal to generate AWB numbers and print packing labels along with the packing list. which can then be pasted on to the packs either manually or by integrating with a label applicator
Loading
- The SKUs / Packs are the loaded into the vehicle
Invoicing
- Post loading, the system is ready to invoice the consignment
- Based on configuration, Tax Invoice will get generated either:
- Within the system
- Or by integrating to government portals to generate
- eInvoice and
- eWaybill Number
- The generated Tax Invoice is printed automatically along with the eWaybill and Packing List
Dispatch
- Post invoicing, the vehicle reaches the security gate
- A license plate reader reads the license plate of the vehicle automatically and pulls up the details of the vehicle in the system
- The security person verifies the details in the system against the physical documents, records important checklist parameters and completes the vehicle out process and generates a Gate Out-Pass
- An automatic mail notification is shared to the customer about the status of delivery
Proof of Delivery
- The final part of the dispatch process is to record the proof of delivery
- The delivery partner uses the POD app to record the date and time of delivery. Apart from date and time the following information is captured
- Condition of the goods
- Received By
- Phone Number and
- Signature
- The recorded POD is then automatically updated against the order
Conclusion
A good WMS not only eases operational load, but also ensures that operations are carried out in the most efficient and optimal way possible. The WMS provides visibility to critical data at the right time to ensure a smooth decision making. The WMS should be capable of handling all the operations/processes described above along with tracking various SKU attributes, such as, Batch Number, Serial Number, Expiry Date, Manufacturing Date or combinations of multiple attributes. In addition the WMS should offer capabilities in terms of:
- Configurable flows
- Location Management
- Allocation Management
- Multiple modes to carry out the same operation (Web UI/HHT/Excel Upload/CSV Upload)
- Tools to visualize KPIs for optimizing warehouse operations
Click on below button to know the list of built in KPI’s that a good WMS should provide.